WP2: Process numerical modeling and multifunctional prototypes design
The WP2 several key advancements in simulation, modeling, and quality assurance for ATL (Automated Tape Laying) and FFF (Fused Filament Fabrication) processes:
- Process Specifications and Simulation Tools: We gathered comprehensive process specifications, enabling the MODA (Modeling Data) specification of applicable simulation tools.
- Machine Vision & Topological Data Analysis (TDA): Machine vision combined with TDA has been applied for the identification and quality assurance of ATL panels.
- Data- and Physics-Based Modeling: A combined approach using data- and physics-based modeling has been developed to calculate intimate contact conditions and heat transfer through ATL panels.
- Thermal and Distortion Modelling: Thermal models for the FFF process and distortion models for ATL-FFF structures were developed to predict composite panel deformation and improve accuracy.
- Integrated Modeling Capabilities: The integration of physics- and sensor-based modeling capabilities, developed in WP6 and WP7, provides efficient prediction of composite panel distortion and ensures better process control.
These advancements form the basis for future improvements in composite panel production, enabling more accurate, reliable, and efficient manufacturing processes.
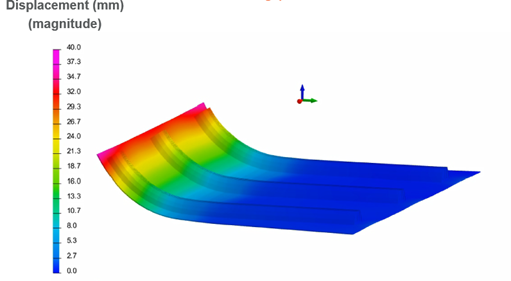
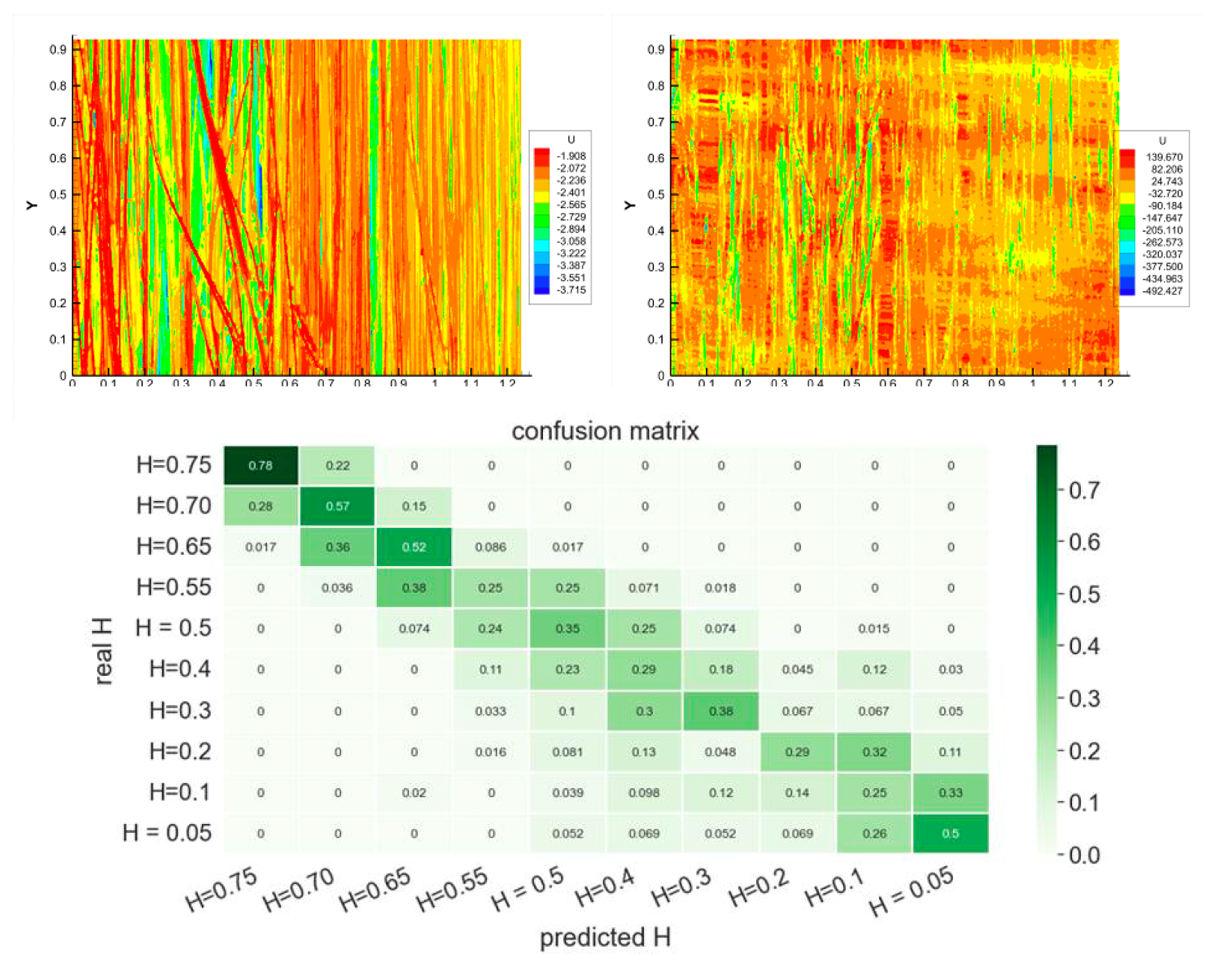
WP3: Functional materials engineering and manufacturing systems
The WP3 made significant advancements in the development of high-performance thermoplastic composites and innovative manufacturing technologies, focusing on debonding-on-demand and efficient repair methods for future applications. Key outcomes include:
- PAEK Nanocomposites for Induction Heating: High-performance PAEK nanocomposites were developed with optimal concentrations of magnetic nanoparticles, enabling induction heating for on-demand debonding applications. These materials can be used for rapid joining, repair, and disassembly of composite structures.
- Debonding Zones in Laminated Composites: Discrete debonding zones were successfully integrated into sandwich-structured laminate composites, produced using Automatic Fiber Placement (AFP) and extrusion-based Additive Manufacturing (AM) technologies, facilitating controlled separation of layers.
- Maintenance, Repair, and Overhaul (MRO) Technologies: New technologies for rapid, on-demand joining, repair, and disassembly of thermoplastic composites were developed, contributing to more efficient MRO operations in various industries.
- Multifunctional Filaments: Multifunctional filaments were created for additive manufacturing, including CNT-integrated FFF filaments for structural health monitoring (SHM) and deicing, as well as magnetic nanoparticle-reinforced filaments for localized heating and product disassembly at the end of life.
- Laser-Assisted Robotized 3D Printing: Laser-assisted robotized FFF processes for high-performance continuous fiber-reinforced 3D printing were established, enhancing the production of next-generation smart composites.
- nduction Heating for Debonding: IA custom experimental setup and induction coil were designed to optimize the induction heating process parameters, enabling effective layer separation in laminated composites.
The combination of advanced materials and automated manufacturing processes demonstrates the potential of additive manufacturing and thermoplastics for next-generation aircraft structures. The project also contributes to the development of sustainable techniques for recycling and repair, addressing growing industrial needs for easily dismantled bonded structures
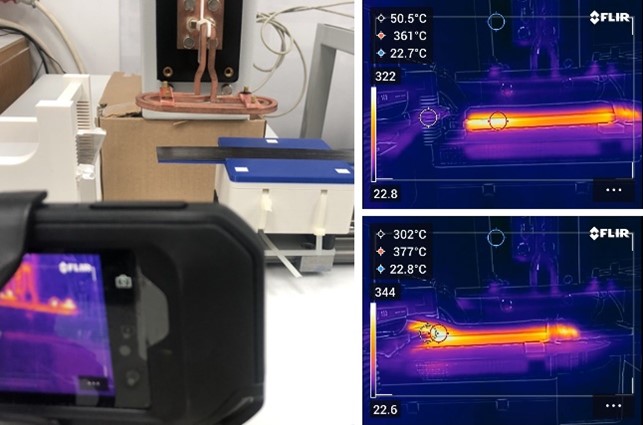
WP4: On-line process control for high-quality automated manufacturing
Work Package 4 focused on the development and integration of advanced technologies for 3D printing high-performance thermoplastics using metal powder-based nozzle and dome components. The key innovations and outcomes include:
- Metal Nozzle and Dome for High-Performance Thermoplastics: Partners developed a monitoring nozzle and a 3D-printed dome in metal powder, designed to print high-performance thermoplastics at room temperature, reducing the risk of electronic degradation due to high temperatures.
- Integration with ATL Robot: These components were successfully integrated into an ATL (Automated Tape Laying) robot for larger part production. Two systems were developed: a laser heating system for in-situ consolidation of continuous fiber ATL tape, and an ultrasound-based defect detection system for non-destructive inspection.
- Laser Scanning and Ultrasound Inspection: A laser scanning system was implemented to control thermal inputs during the printing process, while a non-contact air-coupled ultrasound system (developed by DASEL) provided real-time defect detection during printing.
- ptimized Nozzle Design: OA thermal study of the nozzle and dome was conducted to optimize their shape, ensuring that filament extrusion and deposition occurred without deformation. This refinement enabled the successful printing of specimens that exhibited performance characteristics similar to injection-molded parts.
- Real-Time Monitoring and Defect Detection: A database was created to store live photos from thermal and optical cameras, which were analyzed by algorithms to detect defects during printing, improving quality control.
- Gyroid Structure Demonstrator: A 3D-printed gyroid structure, produced in nearly three hours without interruption, showcased the potential of the integrated technologies for continuous, high-quality manufacturing.
- Zero-Defect Manufacturing Potential: The combination of inline inspection, optimized heating systems, and tailored nozzle designs demonstrates the potential for zero-defect additive manufacturing (AM) of thermoplastic structures. Advanced digitalization and control of heating profiles, with the ability to adjust power within a single scan line at 20Hz, contribute to improved precision.
These advancements highlight the potential of additive manufacturing technologies to optimize the production of high-performance thermoplastic structures, paving the way for more reliable, cost-effective, and scalable manufacturing processes.
WP5:Sensor development and SHM of multifunctional composite laminates
WP5 focused on developing and integrating innovative deformation sensors based on carbon nanotube (CNT) fibers into multifunctional composite laminates. These sensors enable real-time monitoring of structural health, advancing the aerospace sector's capabilities in detecting and addressing damage in critical components.
- Carbon Nanotube (CNT) Fiber Sensors: Successfully embedded CNT sensors into thermoplastic laminates, offering high strain sensitivity without impacting the structural integrity.
- Digital Twin Technology: Developed a digital twin for real-time impact damage detection, allowing the system to analyze strain signals from the sensors and predict potential damage.
- Wireless Data Transmission: Designed a compact, energy-efficient wireless module for real-time transmission of sensor data to an IoT platform, enabling continuous monitoring.
- Advanced Damage Detection:A custom neural network-based algorithm was trained using FEM simulations to detect damage from sensor data, improving accuracy and efficiency.
- Scalable and Lightweight Design: The embedded CNT sensors and wireless technology do not add significant weight to the structure, making them ideal for aerospace applications where minimizing weight is crucial.
This research significantly enhances the state-of-the-art in aerospace monitoring systems, allowing for better maintenance, reduced downtime, and increased safety. The use of real-time monitoring and smart structures offers a transformative approach to how aerospace components are managed, extending their operational life.
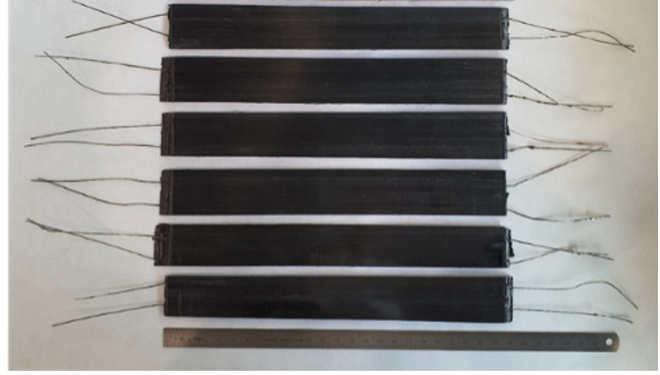
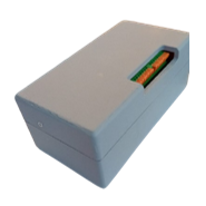
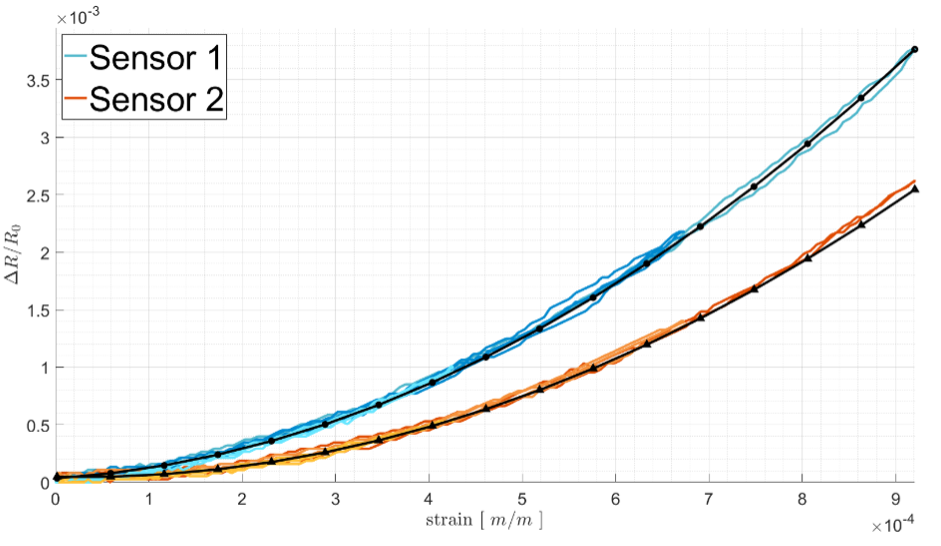
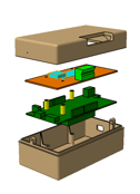
WP6: Laboratory integration and data pipeline realization
Work Package 6 focused on the creation of the Hybrid Twin Platform (HTP) to manage the Multidisciplinary Design Optimization (MDO) process, incorporating both simulation and experimental data from WP3, WP4, WP5, and WP6. Key outcomes include:
- Hybrid Twin Platform (HTP) Development: The HTP was created to manage MDO processes, integrating experimental data from multiple work packages. It supports data collection, analysis, and optimization based on predefined workflows and goals, ensuring full traceability throughout the system.
- Data Visualization for HTP: A data visualization tool was implemented to facilitate clear interpretation of data within the HTP, allowing for real-time monitoring and decision-making.
- Manufacturing of Structural Demonstrators: Two structural demonstrators were manufactured, featuring designs by BAE and ACITURRI. These stiffened panels combined in-situ consolidation of LMPAEK laminates with FFF (Fused Filament Fabrication) of gyroid structures using PEKK.
- Manufacturing of Functional Demonstrators: Three functional demonstrators were produced, showcasing:
- SHM (Structural Health Monitoring) with integrated sensors located by FFF.
- Deicing capabilities with integrated circuits via FFF.
- Disassembly demonstrations featuring integrated inductors for controlled separation.
- Modular HTP Capabilities: The modular HTP supports a variety of use cases, software, and hardware, demonstrating flexibility and adaptability across different applications.
- Demonstration and Testing of Thermoplastic AM Products: The materials and manufacturing setups were validated with a focus on full thermoplastic additive manufacturing (AM) products, providing an initial baseline for further optimization.
- Digitalization and Data-Driven Optimization: The manufacturing cell was digitalized, enabling systematic, data-driven optimization of processes, materials, and product designs. The semi-automated creation of a digital thread ensures that all steps are traceable and linked within the system.
- Robust Manufacturing: High-performance thermoplastics were manufactured using automated FFF and ATL (Automated Tape Laying) processes, demonstrating the platform’s ability to produce complex, robust composite structures.
This work paves the way for optimized, fully digitalized, and traceable additive manufacturing of thermoplastic composites, improving both product quality and production efficiency.
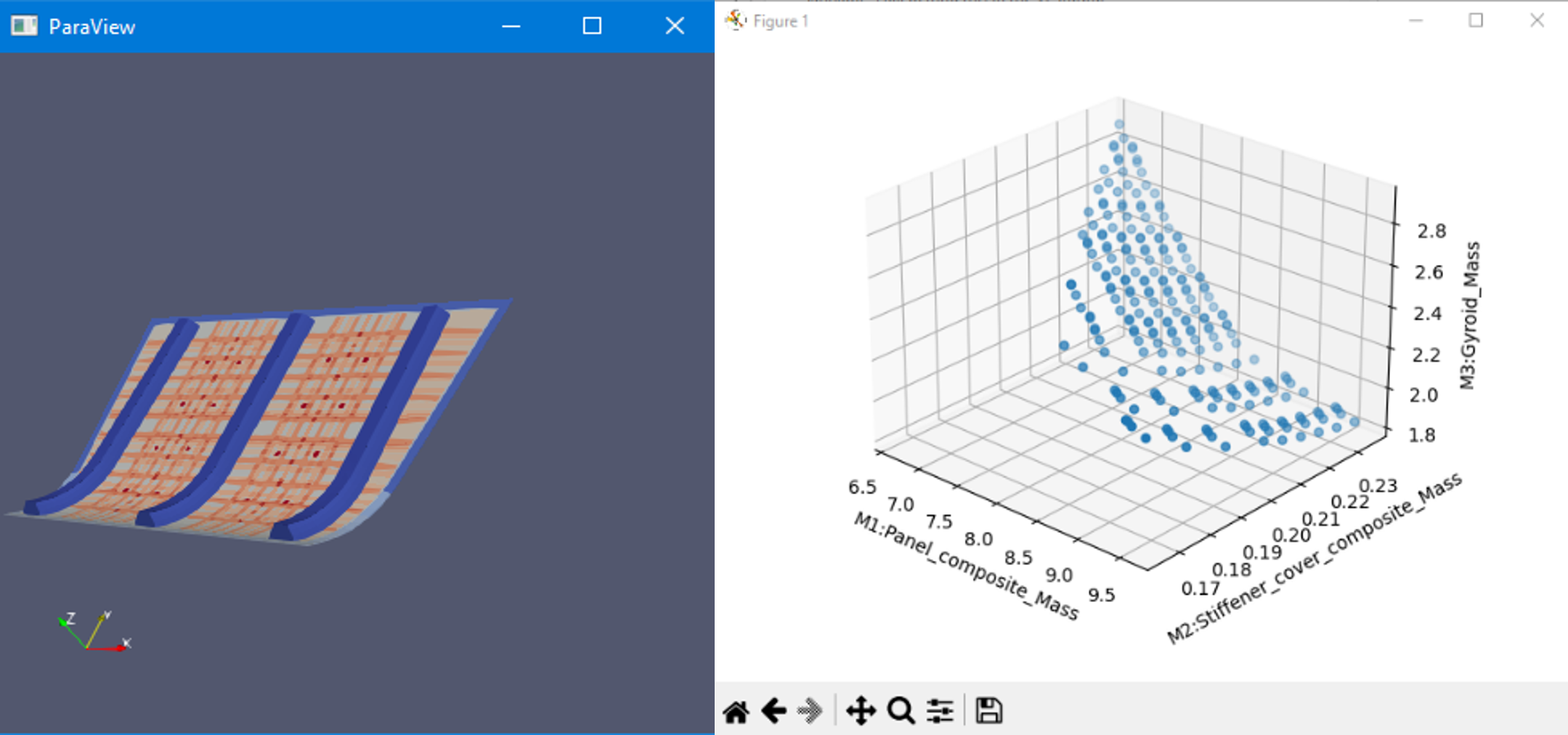
WP7: Multidisciplinary optimization and virtual certification
Work Package 7 focused on combining physics-based and data-driven models within a Multidisciplinary Design Optimization (MDO) framework to address performance requirements, manufacturing constraints, repair strategies, Life Cycle Assessment (LCA), and Life Cycle Cost (LCC). Key results include:
- MDO Framework for Sustainability: A comprehensive MDO framework was developed, integrating both physics- and data-based models to optimize designs while balancing performance, manufacturing, and repair considerations. The framework successfully incorporated LCA and LCC, enabling optimization for environmental sustainability and cost-effectiveness. This integration allowed the evaluation of numerous design parameters across multiple domains.
- Linking SHM to MRO: A theoretical framework was created to connect Structural Health Monitoring (SHM) with Maintenance, Repair, and Overhaul (MRO) strategies. This highlights the value of SHM in advancing condition-based repair strategies over traditional scheduled maintenance. New repair techniques were developed, focusing on the disassembly of thermoplastic material systems created within the DOMMINIO project.
- LCA/LCC Database and Optimization: A dedicated database was established to support the LCA and LCC evaluation of the new materials and manufacturing techniques developed in the project. These modules were successfully embedded within the MDO framework, enabling optimization for sustainability and cost reduction in aircraft component design and manufacturing.
- Simulation for Virtual Certification: A roadmap for the development of simulation techniques aimed at virtual certification was proposed. The review of verification, validation, and uncertainty quantification processes ensured that the credibility of simulation models is demonstrated, supporting their use in the certification of aircraft components.
- Sustainable Aircraft Development: By embedding LCA within the MDO framework, sustainable design was prioritized as a key objective in aircraft development. The project rigorously gathered data, elevating the accuracy of LCC/LCA analysis, which had traditionally suffered from data scarcity.
- Collaborative Achievements: The project demonstrated the ability to bring together diverse inputs from multiple partners, achieving tangible deliverables, particularly in integrating LCA and LCC into the MDO framework. This facilitated progress toward sustainable aircraft design and virtual certification.
Overall, WP7 has advanced the use of comprehensive optimization tools, enabling the design of multifunctional aircraft components that are high-performing, cost-efficient, and environmentally sustainable.
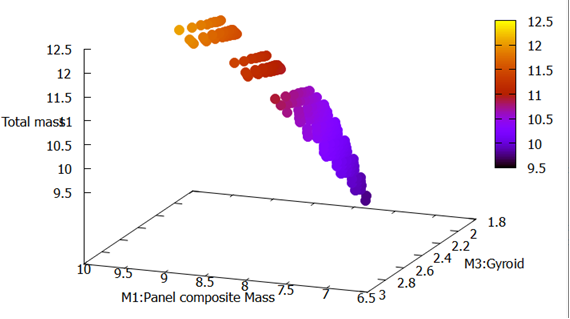